L’acciaio è il materiale più riciclato al mondo e può essere riutilizzato innumerevoli volte senza perdere nessuna delle sue proprietà intrinseche.
Con il nostro ciclo produttivo siamo un esempio importante di economia circolare. Infatti, produciamo acciaio da rottame, evitandone così la dispersione nell’ambiente e riducendo il consumo di materie prime naturali (es. minerale ferroso).
L’acciaio Feralpi è costituito per il 98,6% da materiale riciclato.
I rifiuti e i residui di produzione vengono in massima parte avviati al recupero e/o qualificati come sottoprodotti e solo in parte residuale conferiti in discarica.
Non ci limitiamo alla sola minimizzazione dei rifiuti prodotti, ma adottiamo una visione più ampia che si estende fino alla riduzione della movimentazione di materia prima e rifiuti, alla riduzione di conferimenti, alla sostituzione della materia prima.
Il primo passo verso un modello virtuoso è la riduzione della produzione dei rifiuti. Per questo organizziamo e gestiamo i processi e gli impianti per minimizzare i volumi e monitorare gli impatti.
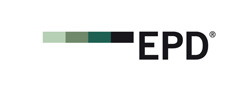
"Life Cycle Assessment" in Feralpi Siderurgica
Feralpi ha implementato metodologie per valutare l’impatto ambientale dei suoi prodotti, utilizzando Life Cycle Assessment, conforme agli standard ISO 14040 e ISO 14044. Questa metodologia esamina tutte le fasi del ciclo di vita del prodotto, dalla materia prima all’uscita del sito aziendale.
Questi studi hanno permesso l’ottenimento di Dichiarazione Ambientale di Prodotto (EPD - Environmental Product Declaration) conformi agli standard ISO 14025 e EN 15804, certificate da organizzazioni indipendenti di terza parte per fornire informazioni verificate sull’impronta ecologica dei prodotti.
In aggiunta alla EPD, Feralpi ha condotto anche studi Carbon Footprint di Prodotto (CFP) per i prodotti di Feralpi Siderurgica, Acciaierie di Calvisano, Presider, Caleotto ed ESF Elbe-Stahlwerke Feralpi GmbH, certificandoli attraverso lo standard ISO 14067. Entrambi gli strumenti, EPD e CFP, forniscono una valutazione completa dell’impatto ambientale, consentendo di comunicare in modo trasparente le prestazioni ambientali dei prodotti e ottenendo un vantaggio competitivo sul mercato. Questi strumenti consentono anche di studiare le emissioni di Scope 3, identificando le aree dove è necessario intervenire lungo la filiera di produzione. Tutti gli studi sono stati soggetti a verifica da enti esterni riconosciuti per garantire l’accuratezza e l’affidabilità dei risultati ottenuti.
Nel nostro percorso verso Zero rifiuti è nato il progetto SteelZeroWaste con l'obiettivo di studiare soluzioni per il miglioramento della sostenibilità ambientale del processo siderurgico attraverso l'implementazione di tecnologie innovative per l'eliminazione degli scarti e riduzione significativa delle emissioni.
Puntiamo alla riduzione totale dei rifiuti attraverso l’abbattimento delle emissioni di CO2 (tramite sequestro e riutilizzo), l’eliminazione degli scarti solidi del ciclo produttivo (e riutilizzo come sottoprodotti per il ciclo interno e per utilizzi esterni). Promuoviamo l’impiego di sottoprodotti di derivazione plastica per il reimpiego di tali materiali e facilitare la riduzione dei materiali plastici nell’ambiente.
-
Scoria nera e bianca
Il recupero delle scorie nere e bianche e la relativa lavorazione sono affidate a ditte esterne che si occupano poi della loro commercializzazione. Presso lo stabilimento di Lonato del Garda, la scoria nera viene trasformata nel prodotto commerciale “Greenstone” con marcatura CE 2+, impiegato nel settore delle costruzioni in sostituzione dei materiali di origine naturale. Esso dispone di una Dichiarazione Ambientale di Prodotto EPD. Anche nello stabilimento di Calvisano la scoria nera viene avviata a recupero per la produzione di prodotti certificati CE 2+. FERALPI STAHL ha iniziato ad impostare le attività necessarie per creare le condizioni di riutilizzo della scoria bianca presso il sito di Riesa, così come avviene in quello di Lonato del Garda.
-
Calore
Lo stabilimento di Feralpi Siderurgica a Lonato del Garda e lo stabilimento di FERALPI STAHL a Riesa recuperano il calore rispettivamente dalle acque di raffreddamento e dal forno di fusione delle acciaierie. L’impianto di Feralpi Siderurgica riscalda gli edifici interni allo stabilimento e, grazie alla collaborazione con l’Amministrazione locale, anche gli edifici pubblici e alcuni privati del territorio comunale. L’impianto in ESF Elbe-Stahlwerke Feralpi GmbH genera fino a 30 t/h di vapore, che viene in parte veicolato dalla locale azienda municipalizzata di Riesa (Stadtwerke Riesa - SWR) direttamente all’azienda Goodyear Dunlop Tires e in parte impiegato per la generazione di energia elettrica. Il calore residuo delle stazioni di compressione viene utilizzato per riscaldare e fornire acqua calda agli uffici dell’amministrazione tecnica di Riesa.
Nel 2023 è stato avviato il progetto di teleriscaldamento presso il sito di Arlenico, che prevede la realizzazione presso il sito di un impianto di produzione di calore attraverso il recupero dei cascami termici derivanti dal processo produttivo di laminazione e un secondo polo nell’area di SILEA a Valmadrera dove il recupero termico avverrà tramite il processo di termovalorizzazione dei rifiuti, sfruttando il calore prodotto dall’impianto attualmente dissipato in atmosfera.
-
Refrattari
Recupero e riutilizzo nel ciclo produttivo dei refrattari esausti al posto della materia prima
I refrattari esausti provenienti da demolizione di siviera vengono reimmessi nel ciclo produttivo, come parziali sostituti di materia prima. La materia prima destinata a essere sostituita è costituita dalla calce calcica e calce dolomitica (“CaO zolle” e “CaO 40%”) il cui utilizzo non comporta alcun impatto negativo sull’ambiente o sulla salute umana.
-
Polveri e fumi
Recupero di polveri e fumi per ridurre la domanda di zinco minerale
Le polveri da abbattimento fumi provenienti dal processo di fusione vengono in gran parte recuperate presso impianti esterni nella componente dello zinco metallico, in sostituzione di quello proveniente da minerale naturale. Le polveri di abbattimento dell’impianto ferroleghe vengono invece immesse direttamente nel ciclo produttivo, con utilizzo pari a quello dei materiali da cui originano.
-
Metalli non ferrosi
Recupero di metalli non ferrosi dalla selezione del rottame
La frazione residua risultante dall’impianto di selezione rottame viene inviata a impianti esterni per il recupero, mediante selezioni meccaniche, di metalli non ferrosi come alluminio, ottone e rame.
-
Scaglia di laminazione
Recupero della scaglia di laminazione, per sostituire il minerale da ferro nella filiera delle costruzioni
La scaglia di laminazione viene avviata al recupero per utilizzo esterno. Il Green Iron è il sottoprodotto proveniente dalla scaglia di laminazione che viene venduta a impianti per la produzione di contrappesi e cemento.
-
Fanghi
Il sito di Lonato di Feralpi Siderurgica ha un nuovo impianto di filtrazione dei fanghi, che permette la produzione di un residuo con minor contenuto di umidità e quindi più adatto a un recupero in ambito edile.
Un passo in più verso la decarbonizzazione.
Il progetto “Polimeri d’Acciaio“, è un’iniziativa che, in collaborazione con i partner i.BLU ed Euromec, ha permesso di sperimentare l’utilizzo di polimeri al posto di carbone e antracite nel processo di fusione.
In questo contesto di economia circolare è strategica la collaborazione con attori della filiera, privati e pubblici, esterni all’organizzazione.
Alcuni dei partner che negli anni ci stanno accompagnando sviluppo di soluzioni circolari sono Enea, Rina, Università degli studi di Brescia, Tenova, Di.ma, I.Blu, Energard, Agroittica, Italghisa, Tecnoproject, Biosyntesy.